Bot the builder: the robot that will replace bricklayers
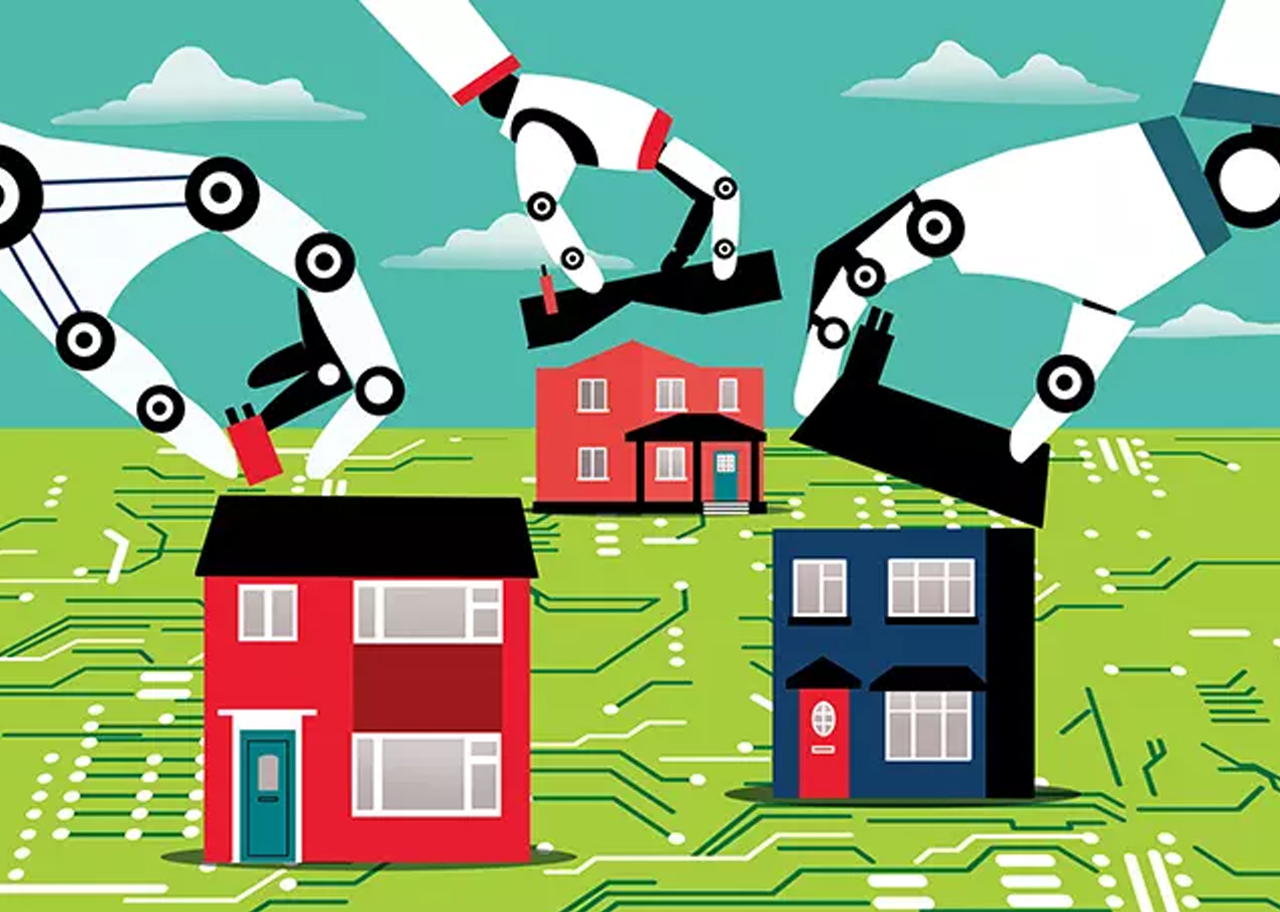
Please use the sharing tools found via the email icon at the top of articles. Copying articles to share with others is a breach of FT.com T&Cs and Copyright Policy. Email licensing@ft.com to buy additional rights. Subscribers may share up to 10 or 20 articles per month using the gift article service. More information can be found at https://www.ft.com/tour.
https://www.ft.com/content/db2b5d64-10e7-11e8-a765-993b2440bd73
About 40 years ago, architect Nate Podkaminer arrived at a building site to find it short of internal wall panels. He couldn’t figure it out; he’d planned meticulously. Then the foreman pointed out something he’d overlooked. Human errors had crept in, resulting in a building 7ft longer than it should be. “With our first robot, on our very first job in 2013, the building was two inches longer than it should have been,” says his son Zak, now operations manager of Construction Robotics, the New York-based company his father co-founded in 2007.
Podkaminer Jr is describing the benefits of the Semi-Autonomous Mason, the Sam100, whose margin of error is now measured in millimetres. A decade in development, the bricklaying robot is currently at work on a handful of building sites across the US. It can apply mortar to any size brick and place one every 8.5 seconds. Where a human mason can lay 300-600 bricks in an eight-hour shift, Sam can lay more than 3,000.
“I can call up all the data on my phone,” enthuses Podkaminer. “I know what time each brick was laid, the weather, temperature and humidity. Down in Virginia we’ve laid 121,000 bricks working 10- to 12-hour days. On our best day, Sam laid 4,100 bricks working 10 hours.” Sam reduces waste, increases accuracy and productivity — and it doesn’t take a tea break. If you believe Podkaminer, it’s the future of construction.
According to a report published last year by McKinsey, the global construction industry is worth $10tn — 13 per cent of world output — and employs 7 per cent of the world’s working-age population. Yet it is at a crisis point: the global population is set to grow, many countries have large housing deficits and there is a shortage of skilled labour. Productivity in construction is not just low but declining in some countries and in the US has halved since the late 1960s. According to McKinsey’s digitisation index, construction is also the least digitised sector in Europe and second least in the US. In short, while there have been great leaps forward in other sectors, construction still largely uses methods that would be familiar to someone working 100 years ago.
So what is the solution? Robots, says Mike Pivac, chief executive of Fastbrick, an Australian tech company. Like Construction Robotics, Fastbrick has developed a bricklaying robot — the Hadrian X. Unlike Sam100, which moves along a track and can only produce straight runs of wall, Hadrian is a truck-mounted robotic arm that, after calibration, can “print” a house using blocks 15 times larger than a regular brick.
“We’ve got a machine that can produce a square metre of wall in 2.5 minutes,” says Pivac, “and a complete house structure in 16 hours.” The nifty part, he says, is its “dynamic stabilisation technology”, which means that the robotic arm can place bricks and other materials more than 100ft away with “sub-millimetre accuracy”, regardless of movement caused by wind or other factors.
Where a human mason can lay 300-600 bricks in an eight-hour shift, Sam can lay more than 3,000
The company has demonstrated a prototype and is nearing completion of two commercial versions. The government of Saudi Arabia has already “put their hand up for the first 100 machines”, says Pivac.
Robots tend to work best in clean, controlled environments. An average building site is the opposite: beset with mud, wind and rain, and overrun with builders, carpenters, electricians, plumbers, plasterers and engineers working on a unique design.
Nonetheless, Pivac envisages the building site of the near future containing multiple crane-mounted robotic arms — some lifting and placing steel beams, others bolting them together, some doing blockwork, others making components using 3D printing.
“If we could flick a switch to 2023,” he says, “you’d see machines working in concert together.” He’s not alone in his forecast. Companies such as JCB, Volvo and Caterpillar are developing autonomous construction vehicles, and start-ups such as Built Robotics in the US, are working on a software retrofit for earthmovers and graders to make them autonomous.
Last June, UK construction giant Balfour Beatty outlined its vision for the future: “The construction site of 2050 will be human-free. Robots will work in teams to build complex structures using dynamic new materials. Elements of the build will self-assemble. Drones flying overhead will scan the site constantly, inspecting the work and using the data collected to predict and solve problems before they arise, sending instructions to robotic cranes and diggers and automated builders with no need for human involvement.”
In some ways, the technology is already here. Many large construction sites use drones to undertake surveys or do tricky jobs such as carrying cables across rivers. Skanska has used 3D printing to produce the cladding shroud on top of the 6 Bevis Marks building in London and robot welders have worked on the $4bn Mario M Cuomo Bridge across the Hudson River, which partially opened last August.
Yet Jeremy Hadall, chief technologist for robotics and automation at the Manufacturing Technology Centre near Coventry in the UK’s Midlands, sounds caution. “People think robots are intelligent. They’re getting better, but they’re still pretty dumb,” he says. Take screwing a nut on to a bolt: a robot would need to know the exact position of the hole, the nut and the bolt and the number of revolutions the nut must be turned. If the hole is out of alignment, the bolt bent or the nut cross-threaded, it would need to have been programmed to solve those issues.
“Robots have a place in building productivity in the construction industry,” he says, “but you have to be realistic about what they can do. Are we going to see completely automated robotic building sites in 10 years? No. In 30 years? Maybe.”
Where Hadall does see room for rapid growth is in modular building, with robots assembling sections of a structure in factories. It’s an area Construction Robotics is already exploring, says Podkaminer. One client is using Sam to make brick panels. Yet productivity isn’t the only goal, he says. Sam can install complex brick patterns more quickly and efficiently than humans, which could allow architects to be more creative without increasing costs.
But with increasingly complex machines entering construction to do what Pivac calls the “dull, dirty and dangerous jobs”, the question on many builders’ lips is: how long until a robot takes my job?
“Our robots haven’t replaced any jobs,” says Podkaminer. “Sam is a collaborative robot.” On one job over the summer, Sam ran 24 hours a day with three, three-man crews of masons and labourers on rotation feeding it with bricks and mortar, pointing the wall, checking quality and placing metal wall ties. How long it is until there are robots to do those jobs, too, is anyone’s guess.
Carl Wilkinson
picture © Nick Lowdnes